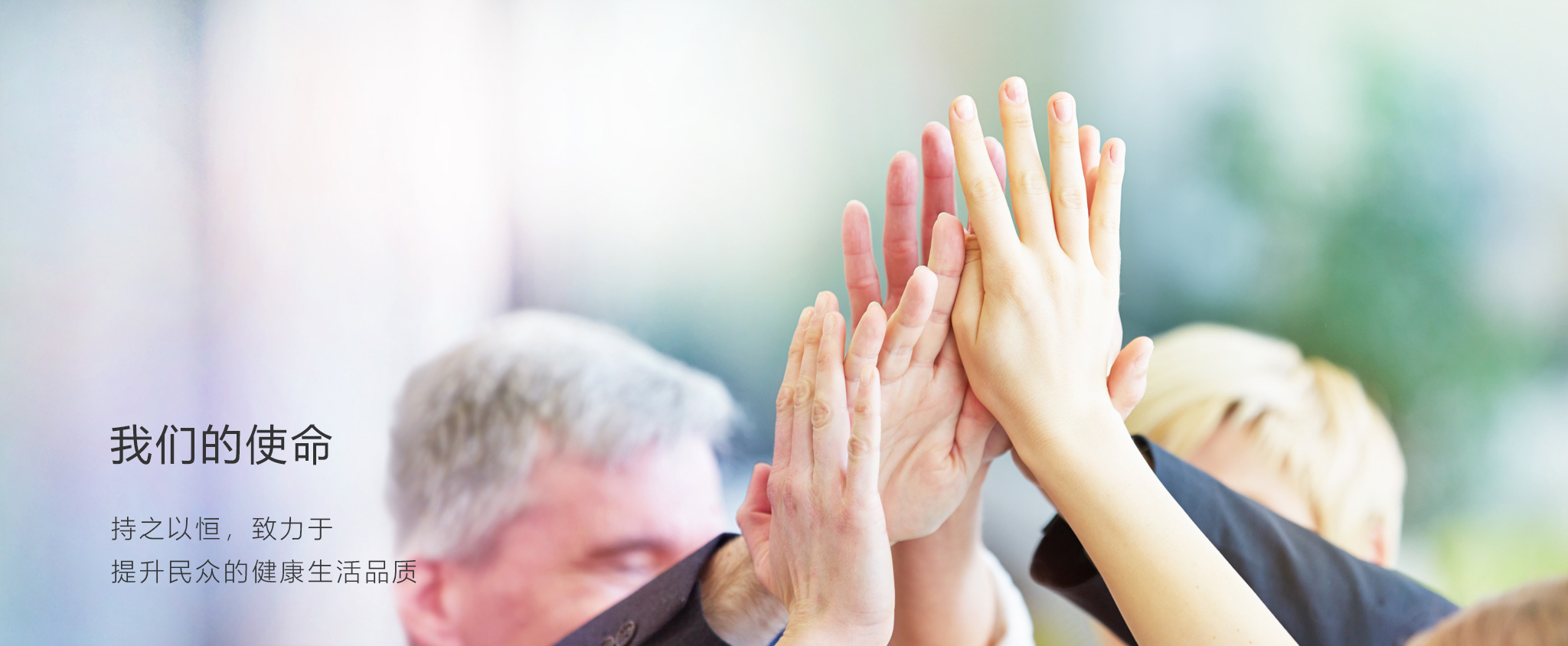
丰田是全球知名的汽车制造商,CPS是丰田公司的缩写,全称翻译为“全面品质管理体系”(Comprehensive Production System)。它是由丰田公司自主研发的一套生产管理体系,是丰田汽车公司在半个多世纪的生产实践中总结出的一种全局性生产控制方法。
凸轮轴位置传感器(Camshaft Position Sensor,CPS)又称为气缸识别传感器(Cylinder Identification Sensor,CIS),为了区别于曲轴位置传感器(CPS),凸轮轴位置传感器一般都用CIS表示。
功用与类型 曲轴位置传感器(Crankshaft Position Sensor,CPS)又称为发动机转速与曲轴转角传感器,其功用是采集曲轴转动角度和发动机转速信号,并输入电子控制单元(ECu),以便确定点火时刻和喷油时刻。
CPS还代表了卡特彼勒生产系统(Caterpillar Production System),这是一个精益生产的概念,致力于改进生产系统的价值流并提升产品质量,与丰田生产系统(Toyota Production System)和富士康生产系统(Foxconn Production System)相似。反应链,即化学链接与物理铆合协同作用,也被称为反应链,与普通链接类型有别。
1、说白了,tps是丰田品牌的一种管理生产方式。其主要特点如下:第一,全公司范围内与“运营”直接相关的改进活动第二,注意事实,能掌握不合格的真正原因第三,管理模式是以站点为中心,管理部门可以为站点提供支持第四,根据经济执行力的判断,不投资的小改进比通过投资的大改进更受重视。
2、丰田管理模式,即著名的丰田生产模式(TPS),其核心理念在于为客户提供卓越的产品和服务。这个理念围绕两个关键点展开:首先,丰田致力于提供高品质的产品,确保每一个环节都注重质量控制,以防止次品进入下一流程,从而确保最终产品的高质量。
3、丰田管理模式,即TPS,是一种卓越的生产与管理方式,其精髓在于使大规模定制下的敏捷产品开发和生产得以实现。这个系统在丰田公司的历史发展中起着关键作用,不仅提升了其核心竞争力,还以高效著称,成为全球企业效仿的管理典范。深入探讨,TPS的管理特点主要体现在其对生产技术的深入研究和实践。
1、丰田式生产管理的关键原则是建立看板体系,强调实时存货,标准作业彻底化,排除浪费、不平及模糊,重复问五次为什么,生产平衡化,充分运用“活人和活空间”,养成自动化习惯,以及弹性改变生产方式。建立看板体系,通过后端顾客需求指导生产,实现零库存,优化流程效率。
2、在工作、操作方法、质量,生产结构和管理方式上要不断地改进与提高。二是消除一切浪费。不能提高附加值的一切工作(包括生产过剩、库存、等待、搬运、加工中的某些活动,复杂的动作,不良的返工等)都是浪费,都应通过全员行为不断加以消除。三是连续改善。这也是当今世界流行的管理思想。
3、---强调实时存货 依据顾客的需求,生产必要的东西,在必要的时候,生产必要的量,这种丰田独创的生产管理概念,在20世纪80年代就已经为美国企业所用,并有很多成功案例。---标准作业彻底化 丰田对生产的内容、顺序、时间控制和结果等所有工作细节都制定了严格的规范,比如装轮胎和引擎需要几分几秒等等。
4、丰田生产系统的关键原则包括: 逆向看板管理: 通过建立看板体系,将生产控制由前端转向后端,工程人员通过看板实时反馈客户需求,实现零库存并提升流程效率。 即时存货原则: 确保只在必要时生产必要的量,减少库存,这是丰田的Just In Time理念,被广泛应用于企业中。
5、流动原则强调生产过程中的顺畅流动,避免中断和等待。拉动原则鼓励企业根据实际需求进行生产,而不是根据预测或计划。最后,持续改进原则要求企业不断寻求改进机会,实现持续性的提升。
1、从管理学的角度来看,丰田召回门事件的主要原因是由于其质量管理体系出现了缺陷。具体来说,以下几个方面的问题可能导致了丰田汽车在全球范围内出现了多次安全问题和大规模召回事件: 质量控制不力:丰田汽车在实施生产时,没有对车辆零部件的品质要求进行严格把关,导致一些安全隐患产品流入市场。
2、召回事件的泛滥与丰田的快速扩张战略脱不了干系,大规模地扩张自然要有与之配套的人才管理、质量管理、产品设计、技术研发,但丰田显然在这几方面都做得不到位。
3、自主管理,以提高质量的保证。为了提升质量方面的快速反应能力,丰田汽车在总部成立了“全球产品质量特别委员会”。